Lith Corporation, founded in 1998 by a group of material science doctor from Tsinghua University, has now become the leading manufacturer of battery lab&production equipment. Lith Corporation have production factories in shenzhen and xiamen of China.This allows for the possibility of providing high quality and low-cost precision machines for lab&production equipment,including: roller press, film coater,mixer, high-temperature furnace, glove box,and complete set of equipment for research of rechargeable battery materials. Simple to operate, low cost and commitment to our customers is our priority.
Perovskite Solar Cell Fabrication Line: Definition, Components, Processes, and Key Considerations
A perovskite solar cell fabrication line refers to an integrated system of equipment and processes designed to produce perovskite solar cells (PSCs) at scale. These lines are essential for transitioning PSC technology from laboratory-scale research to industrial-scale manufacturing. By automating and optimizing the fabrication process, these lines aim to achieve high throughput, consistent quality, and cost-effective production.
In this article, we will explore the definition, components, processes, and key considerations involved in setting up a perovskite solar cell fabrication line.
---
●What Is a Perovskite Solar Cell Fabrication Line?
A perovskite solar cell fabrication line is a series of interconnected machines and tools that automate the production of perovskite solar cells. It includes systems for material deposition, thermal treatment, encapsulation, and testing. The goal of such a line is to ensure uniformity, scalability, and reliability in the mass production of PSCs while maintaining high efficiency and stability.
---
●Components of a Perovskite Solar Cell Fabrication Line
A typical perovskite solar cell fabrication line consists of the following key components:
1. Material Preparation Systems
- Chemical Synthesis Units: Prepare precursors for perovskite materials.
- Solution Mixing Systems: Ensure homogeneous mixing of solutions used in solution-based deposition methods.
- Gloveboxes: Provide controlled environments free from moisture and oxygen to handle sensitive materials like perovskites.
2. Layer Deposition Systems
- Spin Coaters: Deposit thin films of perovskite or other solution-based materials onto substrates.
- Slot Die Coaters: Enable continuous film deposition on flexible substrates for scalable manufacturing.
- Spray Coaters: Suitable for large-area deposition of perovskite layers.
- Vacuum Deposition Systems: Used for depositing electron transport layers (ETLs), hole transport layers (HTLs), and metal electrodes.
- Examples: Sputtering systems, thermal evaporators, atomic layer deposition (ALD) systems.
3. Thermal Treatment Systems
- Oven Annealers: Crystallize perovskite films at elevated temperatures.
- Rapid Thermal Processors (RTP): Facilitate fast and uniform heating for improved film quality.
- Vacuum Furnaces: Provide controlled environments for thermal treatments.
4. Encapsulation Systems
- Laminating Machines: Seal solar cells between barrier films to enhance stability and protect against environmental degradation.
- Vacuum Sealing Systems: Ensure airtight seals to prevent moisture and oxygen ingress.
5. Characterization and Testing Systems
- Solar Simulators: Measure current-voltage (I-V) characteristics under standardized light conditions.
- Quantum Efficiency Analyzers: Assess the spectral response of the cells.
- Electroluminescence (EL) Imaging Systems: Detect defects and non-uniformities in solar cells.
- Environmental Chambers: Test durability under varying temperature, humidity, and UV exposure conditions.
6. Automation and Control Systems
- Robotics: Automate material handling, substrate transfer, and alignment processes.
- Process Control Software: Monitor and optimize each step of the fabrication process for consistency and quality assurance.
---Benchtop Plasma Cleaner
●Perovskite Solar Cell Fabrication Process
The fabrication process for perovskite solar cells typically involves the following steps:
1. Substrate Preparation
- Clean and pattern the transparent conductive oxide (TCO) substrate (e.g., FTO or ITO).
2. Electron Transport Layer (ETL) Deposition
- Deposit the ETL using techniques like sputtering, ALD, or spin coating.
- Common ETL materials include TiO₂, ZnO, or SnO₂.
3. Perovskite Layer Deposition
- Use solution-based methods (spin coating, slot die coating, spray coating) or vacuum-based methods to deposit the perovskite absorber layer.
- Optimize the composition and thickness of the perovskite layer for maximum efficiency.
4. Hole Transport Layer (HTL) Deposition
- Deposit the HTL using spin coating, vapor deposition, or other suitable methods.
- Common HTL materials include Spiro-OMeTAD, PEDOT:PSS, or CuSCN.
5. Metal Electrode Deposition
- Deposit the top electrode using thermal evaporation or sputtering.
- Common metals include gold (Au), silver (Ag), or aluminum (Al).
6. Encapsulation
- Seal the solar cell with barrier films or glass to protect it from environmental factors like moisture and oxygen.
7. Testing and Quality Assurance
- Perform electrical and optical characterization to evaluate device performance.
- Conduct environmental testing to assess long-term stability.
---
●Key Considerations for Setting Up a Perovskite Solar Cell Fabrication Line
1. Scalability
- Choose deposition techniques (e.g., slot die coating, roll-to-roll printing) that can be scaled up for large-area production.
2. Uniformity
- Ensure consistent film quality across large substrates to maintain high efficiency and reliability.
3. Cost-Effectiveness
- Optimize material usage and process efficiency to reduce production costs.
4. Stability
- Implement advanced encapsulation techniques and use stable materials to improve the long-term performance of the devices.
5. Safety
- Handle toxic materials (e.g., lead-based perovskites) safely by incorporating proper safety measures and waste management systems.
6. Automation
- Integrate robotics and process control software to minimize human error and increase throughput.
7. Environmental Control
- Maintain controlled environments (e.g., gloveboxes, humidity chambers) to prevent degradation of sensitive materials during fabrication.
---
●Challenges in Perovskite Solar Cell Fabrication Lines
1. Material Sensitivity:
- Perovskite materials are highly sensitive to moisture, oxygen, and heat, requiring precise environmental control throughout the fabrication process.
2. Uniformity at Scale:
- Achieving uniform film quality over large areas remains a significant challenge, especially for solution-based deposition methods.
3. Lead-Free Alternatives:
- Developing environmentally friendly, lead-free perovskite materials without compromising efficiency is a critical area of research.
4. Encapsulation:
- Designing effective encapsulation methods to ensure long-term stability under real-world conditions is essential.
5. Reproducibility:
- Ensuring consistent performance across batches requires strict process control and standardization.
---
●Future Trends in Perovskite Solar Cell Fabrication Lines
1. Roll-to-Roll Manufacturing:
- Develop continuous roll-to-roll processes for producing flexible and lightweight perovskite solar cells on plastic substrates.
2. Lead-Free Materials:
- Innovate new perovskite compositions that eliminate toxic elements like lead while maintaining high efficiency.
3. Tandem Solar Cells:
- Integrate perovskites with silicon or other materials to create tandem solar cells with record-breaking efficiencies.
4. AI and Machine Learning:
- Use AI-driven algorithms for process optimization, defect detection, and predictive maintenance in fabrication lines.
5. Sustainability Focus:
- Design fabrication lines that minimize waste, reduce energy consumption, and promote environmentally friendly practices.
---
●Conclusion
Perovskite solar cell fabrication lines are crucial for scaling up the production of this promising photovoltaic technology. By integrating advanced equipment, automation, and process control, these lines enable the mass production of high-efficiency, stable, and cost-effective perovskite solar cells. Addressing challenges related to material sensitivity, uniformity, and scalability is essential for realizing the full potential of perovskite solar cells in the renewable energy market.
What advancements in perovskite solar cell fabrication lines excite you most? Share your thoughts below! Together, let’s explore how these innovations are shaping the future of clean energy.
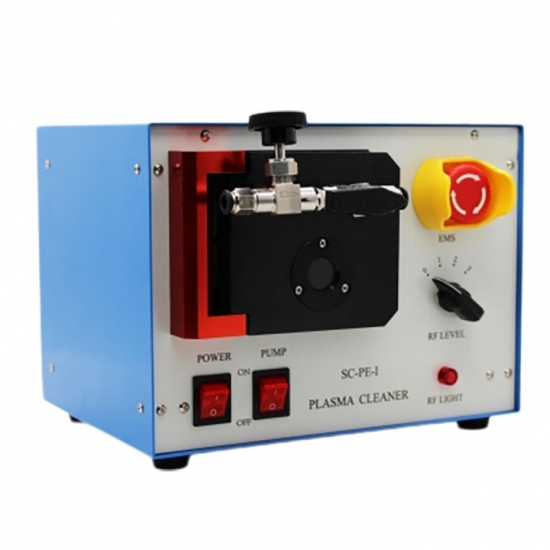