Button Cell Assembly: A Comprehensive Guide
Button cells, also known as coin cells, are small, round batteries commonly used in a variety of compact electronic devices like watches, calculators, hearing aids, and medical devices. The assembly of button cells involves precise and detailed processes to ensure reliability and performance. This guide outlines the essential steps, equipment, advantages, and challenges involved in button Cell fabrication.
Key Components of Button Cells
Cathode: Typically made from materials such as manganese dioxide, silver oxide, or lithium compounds.
Anode: Commonly composed of zinc or lithium.
Separator: A porous membrane that prevents the electrodes from touching each other while allowing ionic movement.
Electrolyte: A conductive medium that facilitates the flow of ions between the anode and cathode.
Casing: The metal casing that houses the cell components, consisting of a top (positive terminal) and a bottom (negative terminal) part.
Steps in Button Cell Research
1. Electrode Preparation
Mixing: The active materials for the anode and cathode are mixed with binders and conductive agents to form a slurry.
Coating: The slurry is coated onto a metallic foil, which serves as the current collector. The anode material is coated onto copper foil, while the cathode material is coated onto aluminum foil.
Drying: The coated electrodes are dried to remove solvents and solidify the active material onto the foil.
Punching/Cutting: The dried electrodes are punched or cut into small discs to fit into the button cell casing.
2. Assembly
Anode Insertion: The anode disc is placed into the bottom part of the metal casing.
Separator Placement: A separator disc is placed on top of the anode to prevent direct contact with the cathode.
Cathode Insertion: The cathode disc is placed on top of the separator.
Electrolyte Filling: The electrolyte is added to the cell to ensure the ionic movement between the anode and cathode.
Sealing: The top part of the casing is placed over the assembly and sealed using crimping or welding to ensure the cell is airtight and leak-proof.
3. Testing and Quality Control
Electrical Testing: Each cell is tested for voltage, internal resistance, and capacity to ensure it meets the required specifications.
Leak Testing: Cells are inspected for electrolyte leakage, which could lead to failure or damage to devices.
Aging: Some cells undergo an aging process where they are stored for a period to stabilize their electrochemical properties.
Equipment Used in Button Cell Assembly
Mixers: For preparing electrode slurries.
Coating Machines: To apply the slurry onto current collector foils.
Drying Ovens: For removing solvents from coated electrodes.
Punching Machines: To cut the electrodes into precise shapes.
Assembly Machines: For placing the electrodes, separator, and electrolyte into the casing.
Crimping/Welding Machines: To seal the button cell.
Testing Equipment: For electrical and leakage testing.
Advantages of Button Cell Assembly
Compact Size: Ideal for small electronic devices due to their compact and lightweight design.
Stable Voltage: Provides consistent voltage output, making them reliable for sensitive devices.
Long Shelf Life: Low self-discharge rates ensure a long shelf life.
Variety: Available in different chemistries (e.g., silver oxide, lithium) to suit various applications.
Challenges in Button Cell Assembly
Precision: The small size of components requires precise handling and assembly to avoid defects.
Material Handling: Sensitive materials like lithium and electrolytes require careful handling to prevent contamination and ensure safety.
Sealing: Ensuring an airtight and leak-proof seal is critical to prevent electrolyte leakage and extend the cell's life.
Quality Control: Maintaining consistent quality across large production batches requires rigorous testing and quality control measures.
Development Challenges
Miniaturization: As electronic devices become smaller, there is a continuous push to develop even smaller button cells with higher energy densities.
Material Innovation: Researching new materials that can offer better performance, longer life, and improved safety.
Environmental Concerns: Addressing the disposal and recycling of button cells, particularly those containing heavy metals like mercury.
Cost Reduction: Developing cost-effective manufacturing processes to make button cells more affordable without compromising quality.
Conclusion
Button cell assembly is a meticulous process that involves several stages, each requiring specialized equipment and precise control to ensure high-quality, reliable batteries. While there are significant advantages to using button cells in compact electronic devices, the challenges associated with precision, material handling, and quality control necessitate continuous innovation and optimization in manufacturing processes. As technology advances and the demand for smaller, more efficient batteries grows, the development of button cells will play a critical role in powering the next generation of electronic devices.
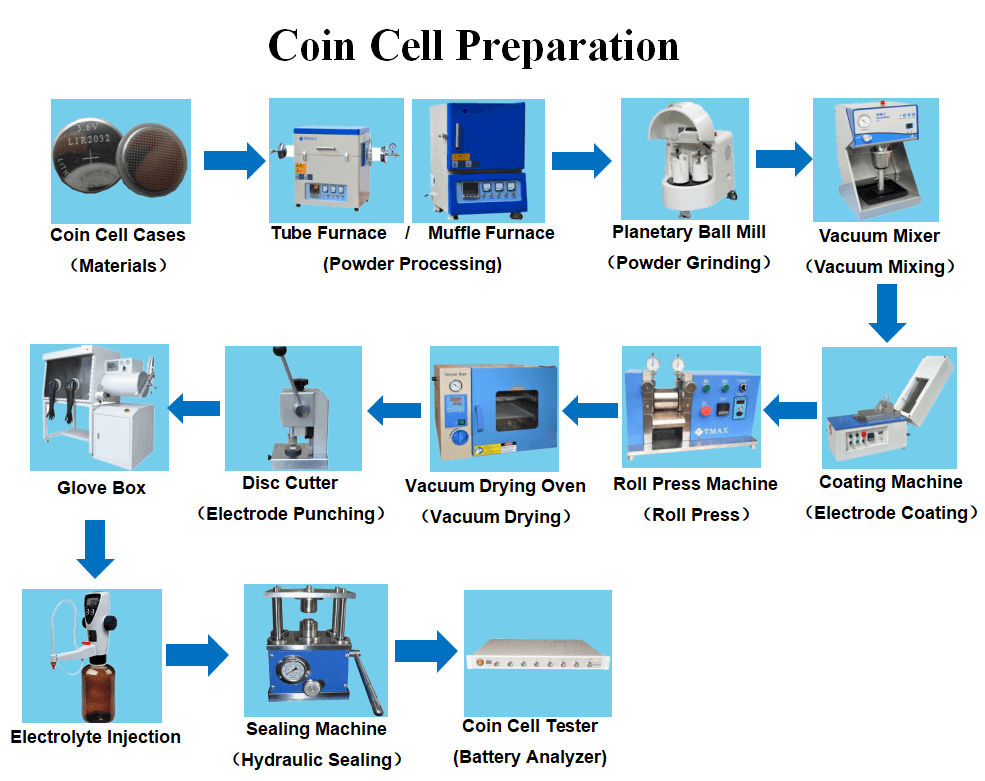